Mastering Quality Control: Machining Inspection Report Template Explained
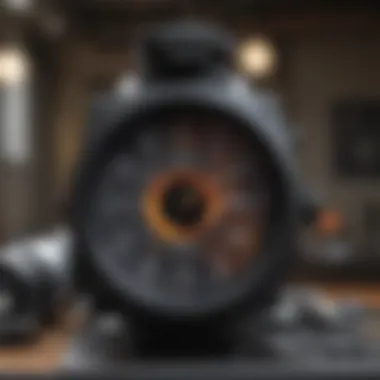
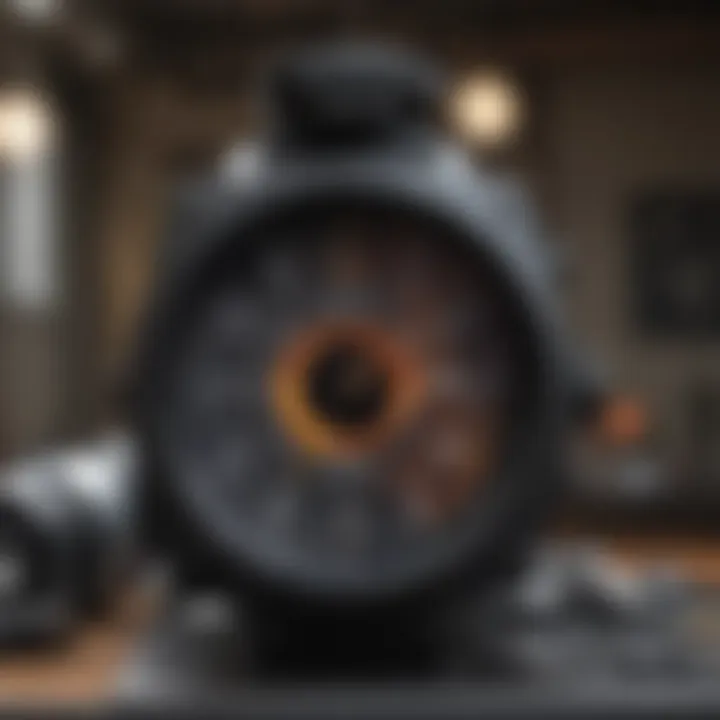
Considerations for Industry Standards Compliance
Significance of Quality Control in Machining Processes
Ensuring Consistency and Efficiency in Inspection Reporting
Introduction
In the intricate realm of machining, the meticulous scrutiny of components is paramount to ensure precision and quality. The ["Introduction"] section of this discourse delves into the fundamental importance of machining inspection, shedding light on its crucial role in upholding industry standards and operational excellence. By elucidating the pivotal aspects and considerations of
Overview of Machining Inspection
Importance of Inspection in Machining Processes
Within the intricate web of machining operations, the ["Importance of Inspection in Machining Processes"] stands tall as a cornerstone of quality assurance and operational efficacy. It holds the power to pinpoint deviations, ensuring adherence to stringent specifications and safeguarding against defects. The key characteristic of ["Importance of Inspection in Machining Processes"] lies in its ability to act as a steadfast guardian of quality, gauging each machined component with unwavering precision. This feature sets it apart as an indispensable tool in the arsenal of precision engineering, boosting efficiency and accuracy in production processes.
Objectives of Machining Inspection
The ["Objectives of Machining Inspection"] segment epitomizes a strategic approach towards achieving flawless machined components. It aims to validate the conformity of each part to predefined standards, mitigating the risks of non-compliance and fostering a culture of meticulous craftsmanship. The essence of ["Objectives of Machining Inspection"] lies in its capability to align production outcomes with quality benchmarks, ensuring consistency and reliability in every machined part. This distinct feature underscores its significance as a linchpin in the pursuit of precision and excellence in machining inspection.
Purpose of the Template
Facilitating Standardized Inspection Procedures
The template's role in ["Facilitating Standardized Inspection Procedures"] is paramount in streamlining the evaluation process, harmonizing disparate inspection practices, and instilling uniformity in reporting protocols. Its key characteristic lies in its ability to establish a common language of inspection, ensuring seamless communication across diverse operational sectors. By promoting a standardized framework, the template nurtures a culture of coherence and precision in inspection methodologies, presenting data in a clear and consistent manner.
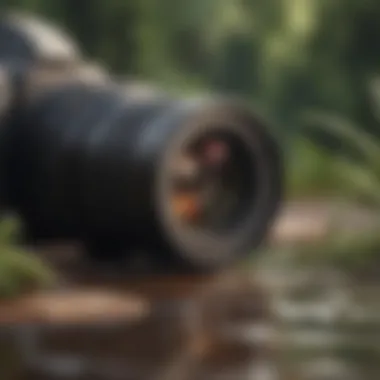
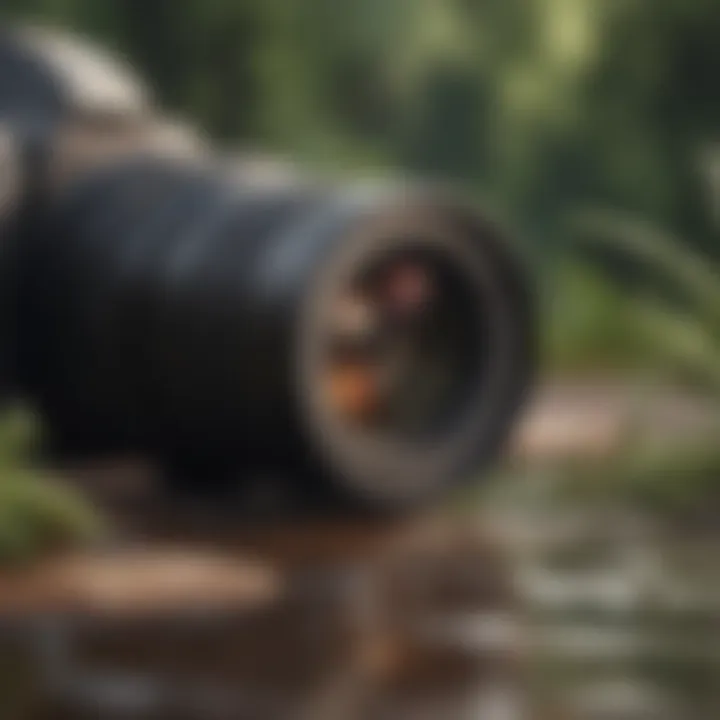
Ensuring Consistency in Reporting
At the core of the template's design is the imperative of ["Ensuring Consistency in Reporting"], a foundational element that underpins the credibility and reliability of inspection findings. Its key characteristic revolves around eliminating ambiguities and variations in reporting styles, fostering a cohesive narrative that illuminates the nuances of each inspection. By upholding a standard format for documentation, the template instills discipline in reporting practices, fortifying the integrity of inspection records and facilitating informed decision-making processes.
Key Components of the Template
In the realm of machining inspection, the Key Components of the Template form the bedrock of structured evaluation and quality assurance. It is essential to grasp the nuances of these components to ensure meticulous inspection practices. The Identification Details section, encompassing crucial information such as the Date of Inspection and Inspector's Name, serves as the gateway to initiating a thorough inspection process. Moreover, the Description of Machined Parts sheds light on the intricate specifications and materials used in the machining process. Understanding the Inspection Criteria, including Tolerance Limits and Surface Finish Requirements, is paramount for upholding quality standards. Additionally, delving into Measurement Techniques like Caliper Measurements and CMM (Coordinate Measuring Machine) Analysis is indispensable for comprehensive inspection protocols.
Identification Details
Date of Inspection
The Date of Inspection holds significant relevance in the meticulous assessment of machined components. By specifying the date of inspection, the inspection report gains temporal context, aiding in tracking the progress of inspections over time. Furthermore, the Date of Inspection enables stakeholders to correlate inspection findings with specific timelines, facilitating efficient decision-making processes. The unique feature of the Date of Inspection lies in its ability to provide a clear chronological record of inspection activities, contributing to the overall comprehensiveness of the inspection report.
Inspector's Name
The inclusion of the Inspector's Name in the inspection report serves as a vital identifier of accountability and expertise. Assigning responsibility to a designated inspector helps in establishing a clear line of ownership for the inspection process. By highlighting the Inspector's Name, the report acknowledges the individual overseeing the inspection, ensuring transparency and accountability. The unique feature of including the Inspector's Name lies in fostering a sense of ownership and professionalism in the inspection process, enhancing the credibility and reliability of the inspection report.
Description of Machined Parts
Specifications
Specifications play a pivotal role in delineating the exact requirements and standards that machined parts must adhere to. By detailing specifications in the inspection report, stakeholders gain a comprehensive understanding of the expected attributes of machined components. Highlighting specifications helps in aligning inspection procedures with quality benchmarks, fostering accuracy and precision in evaluation. The unique feature of specifications lies in providing a detailed roadmap for inspecting machined parts, guiding inspectors towards meticulous assessment and compliance with industry standards.
Material Used
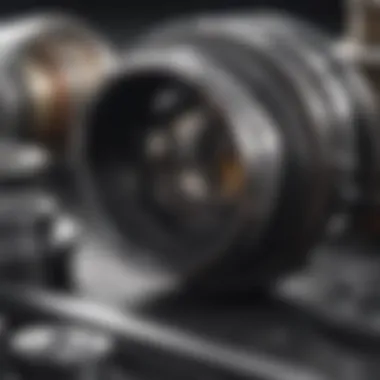
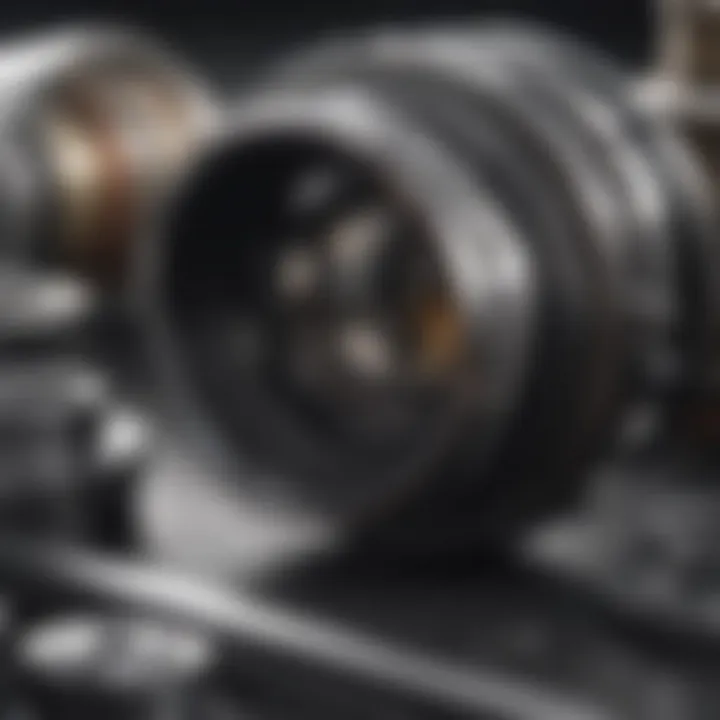
The material used in machining processes significantly influences the quality and performance of machined parts. By specifying the materials used in the inspection report, stakeholders gain insight into the fundamental composition of machined components. Highlighting the material used aids in identifying material-specific inspection criteria and considerations, ensuring thorough evaluation of material integrity. The unique feature of detailing the material used lies in guiding inspection procedures tailored to specific material characteristics, enabling targeted assessments and quality control measures.
Inspection Criteria
Tolerance Limits
Tolerance limits define the permissible deviation from specified dimensions or parameters in machined parts. Understanding tolerance limits is vital for discerning quality variations and ensuring conformance to precise measurements. Highlighting tolerance limits in the inspection report delineates the acceptable ranges for dimensional accuracy, guiding inspectors in identifying deviations and potential non-conformities. The unique feature of tolerance limits lies in facilitating precise quality assessments, enabling inspectors to uphold stringent quality standards and address discrepancies effectively.
Surface Finish Requirements
Surface finish requirements specify the desired surface texture and quality standards for machined parts. Emphasizing surface finish requirements in the inspection report aids in evaluating the visual and tactile attributes of machined surfaces. By outlining surface finish requirements, inspectors can assess the surface quality in alignment with specific criteria, ensuring consistency and adherence to specified standards. The unique feature of surface finish requirements lies in enabling inspectors to validate the aesthetic and functional properties of machined parts, enhancing overall quality control measures.
Measurement Techniques
Caliper Measurements
Caliper measurements comprise precise dimensional assessments using calipers, enabling inspectors to determine accurate sizing and dimensions of machined parts. By leveraging caliper measurements, inspectors can conduct detailed dimensional evaluations, ensuring compliance with specified design parameters. Highlighting caliper measurements in the inspection report facilitates quantitative analysis of machined components, aiding in identifying dimensional accuracies and potential deviations. The unique feature of caliper measurements lies in providing a straightforward and reliable method for dimensional inspections, enhancing the precision and reliability of measurement data.
(Coordinate Measuring Machine) Analysis
CMM analysis entails advanced dimensional inspection using coordinate measuring machines to capture intricate geometrical data of machined parts. By utilizing CMM analysis, inspectors can achieve comprehensive 3D measurements and geometric evaluations, facilitating complex inspections with high precision. Describing CMM analysis in the inspection report underscores the use of sophisticated measurement technology, optimizing inspection accuracy and efficiency. The unique feature of CMM analysis lies in delivering detailed and reliable geometrical insights, enabling inspectors to conduct in-depth dimensional analyses and geometric verification with advanced precision.
Implementation Guidelines
Conducting the Inspection
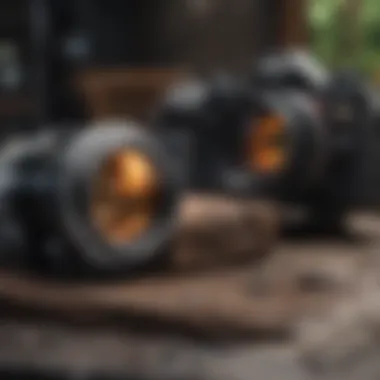
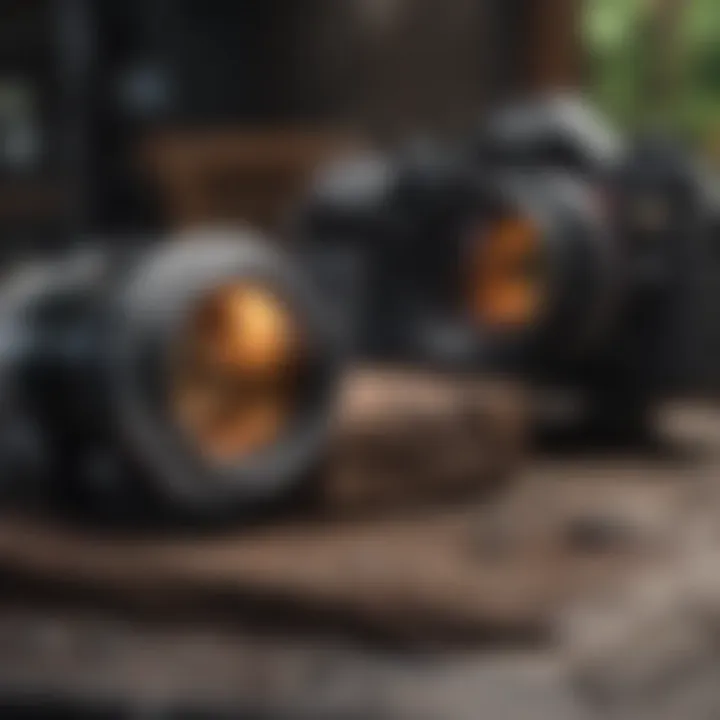
Step-by-Step Inspection Process
Delving into the intricacies of the Step-by-Step Inspection Process, this methodical approach offers a systematic way to conduct inspections with precision and accuracy. Each step within the process is meticulously designed to cover every aspect of the inspection procedure, from initial assessments to final evaluations. By breaking down the inspection into manageable steps, the Step-by-Step Inspection Process ensures comprehensive coverage of all critical elements, reducing the likelihood of oversights and enhancing the effectiveness of the inspection.
Documenting Findings
Examining the role of documenting findings in the inspection process, this aspect underscores the importance of maintaining a detailed record of inspection results. Documenting findings involves recording observations, measurements, and any deviations from specified requirements during the inspection. This documentation serves as a crucial reference for evaluating the quality of machined parts, identifying patterns of non-conformities, and facilitating informed decision-making for process improvements.
Identification of Non-Conformities
Focusing on identifying non-conformities, this critical aspect of the inspection process involves recognizing deviations from established quality standards. By pinpointing areas of non-compliance or defects in machined parts, the identification of non-conformities enables swift corrective actions to be implemented, preventing potential defects from progressing downstream in the production cycle. This proactive approach to quality control enhances product quality, compliance with regulations, and overall customer satisfaction.
Conclusion
Significance of Comprehensive Inspection Reporting
Enhancing Quality Control Measures
Venturing into the domain of Enhancing Quality Control Measures sheds light on a fundamental component critical for operational efficacy. This facet plays a pivotal role in elevating quality assurance protocols within machining processes, fostering precision and reliability in product outputs. The distinguishing trait of Enhancing Quality Control Measures lies in its ability to enforce stringent standards and mitigate deviations, ensuring conformity to established benchmarks. As a favored choice in this narrative, its inherent emphasis on accuracy and consistency resonates profoundly, fortifying the foundation of comprehensive inspection reporting. The unique strength of Enhancing Quality Control Measures lies in its unwavering commitment to upholding product quality while pinning down operational inconsistencies, thereby fortifying the fabric of this article.
Improving Process Efficiency
Exploring the landscape of Improving Process Efficiency unravels a key driver paramount to the overarching goal of operational optimization. This facet contributes significantly to enhancing workflow dynamics and resource utilization within machining environments, fostering productivity and timeliness. At its core, the defining attribute of Improving Process Efficiency lies in its ability to streamline operations and eliminate redundancies, propelling efficiency gains and cost-effectiveness. Its prominence in this discourse stems from its reputation as a sought-after strategy that propels operational efficacy while minimizing resource wastage. The distinctive feature of Improving Process Efficiency lies in its agile nature, adapting seamlessly to evolving operational needs and aligning with the strategic imperatives outlined in this article.
Future Implementations
Incorporation of Digital Inspection Technologies
Delving into the domain of Incorporation of Digital Inspection Technologies unearths a transformative facet poised to revolutionize inspection methodologies within machining realms. This component contributes significantly to enhancing inspection accuracy and data-driven decision-making processes, ushering in a new era of precision and efficiency. The pivotal characteristic of this incorporation lies in its capacity to harness cutting-edge technologies for real-time data analyses and visualization, amplifying inspection capabilities and ensuring real-time insights. As a preferred choice in this context, its integration heralds a paradigm shift towards digitized inspection frameworks, delivering unparalleled advantages in terms of speed, accuracy, and data integrity. The standout feature of Incorporation of Digital Inspection Technologies resides in its potential to revolutionize traditional inspection paradigms and set new benchmarks for inspection excellence within machining environments.
Continuous Improvement Strategies
Embarking on an exploration of Continuous Improvement Strategies unveils a strategic approach indispensable for sustained growth and operational refinement. This aspect plays a pivotal role in fostering a culture of innovation and adaptability within machining operations, nurturing a mindset of continual evolution and enhancement. The salient characteristic of Continuous Improvement Strategies lies in its structured methodology for identifying bottlenecks, addressing inefficiencies, and instituting iterative enhancements throughout the operational lifecycle. Selected for its resonance with the overarching objectives of this article, this strategy stands out as a beacon of progressive thinking that drives operational excellence and long-term sustainability. The defining feature of Continuous Improvement Strategies lies in its agile framework, enabling organizations to pivot swiftly in response to market dynamics and internal performance indicators, thereby cementing its status as a strategic imperative within machining inspection and reporting frameworks.