Unleashing Peak Performance: A Deep Dive into Industrial Machinery Repair Strategies
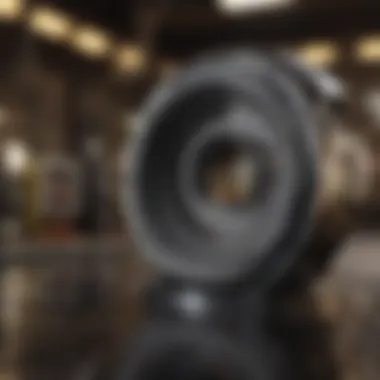
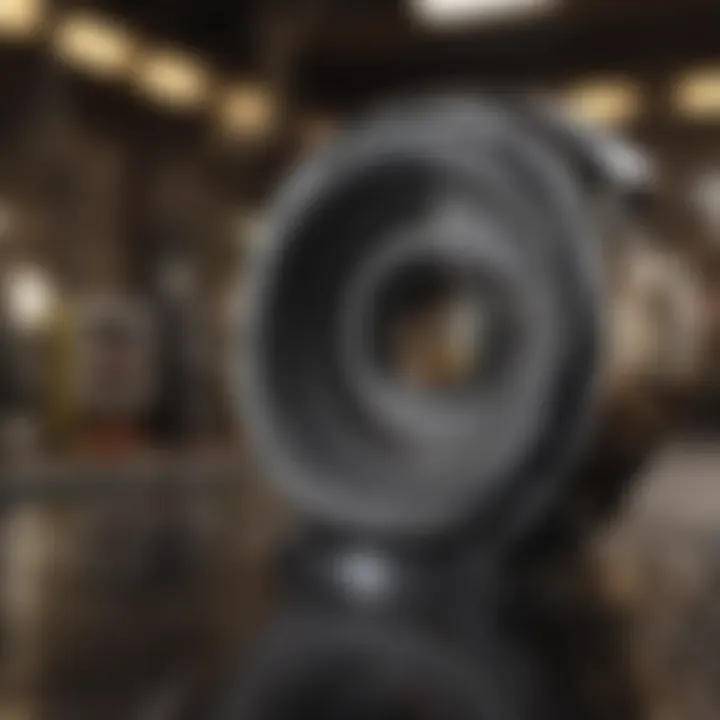
Overview of the Topic
In the realm of industrial machinery repair, the quest for maximizing efficiency stands as a paramount objective. The intricate interplay between performance optimization and equipment longevity serves as the cornerstone of this discipline. Delving deep into the nuances of diagnostic procedures and proactive maintenance, this comprehensive guide unveils a trove of strategies dedicated to ensuring the smooth and seamless operation of heavy-duty machinery.
Current Status and Challenges
Amidst the industrial landscape, the current state of machinery maintenance poses several intricate challenges. The relentless demands on heavy-duty equipment coupled with the pressures of operational efficiency create a landscape fraught with obstacles. From the complexities of on-the-spot repairs to the intricacies of preventive maintenance scheduling, industrial machinery repair stands at a crossroads where every decision holds weighty consequences for operational continuity.
Sustainable Solutions
Navigating the labyrinth of challenges in industrial machinery repair requires a steadfast commitment to sustainable solutions. From embracing advanced diagnostic technologies to fostering a culture of proactive equipment care, the journey towards efficiency hinges on eco-conscious practices. By showcasing successful case studies and exemplifying effective resource management, the pathway towards streamlined and sustainable machinery repair emerges as a beacon of hope amidst the industrial tumult.
Impact and Importance
The ramifications of industrial machinery repair resonate far beyond the confines of factory walls. Delving deeper, the analysis unfurls the impact of efficient repair practices on ecosystems, communities, and future generations. Emphasizing the vital importance of conservation efforts and sustainable resource use, this guide underscores the pivotal role machinery efficiency plays in shaping a more eco-friendly and operationally sound industrial landscape.
Understanding Industrial Machinery Repair
Industrial machinery repair is a critical aspect of ensuring operational efficiency and longevity in industrial settings. The meticulous maintenance and timely repair of heavy-duty equipment play a pivotal role in minimizing downtime, optimizing productivity, and extending the lifespan of machinery. This section serves as a foundational pillar in the holistic approach to industrial machinery care, emphasizing the significance of proactive measures to prevent costly breakdowns and enhance overall performance.
Importance of Timely Repairs
Timely repairs within industrial settings have a direct impact on production efficiency, acting as a linchpin in the seamless operation of machinery. A proactive approach to maintenance not only mitigates the risk of unexpected failures but also safeguards against potential disruptions in the production line. By addressing issues promptly, organizations can streamline operations, reduce downtime, and optimize workflow efficiency, ultimately translating into tangible gains in productivity and output.
Impact on Production Efficiency
The impact of addressing repairs in a timely manner cannot be overstated in the industrial landscape. Swift intervention in rectifying machinery issues ensures continuity in production processes, preventing cascading failures that could hamper overall efficiency. Moreover, implementing timely repairs fosters a culture of preventive maintenance that not only augments production output but also cultivates a proactive approach towards machinery care.
Cost-saving Benefits
Aside from fortifying production efficiency, timely repairs offer substantial cost-saving benefits to organizations. By addressing issues proactively, companies can avoid expensive breakdowns that necessitate extensive repairs or replacements. This strategic expenditure on preventive maintenance translates into long-term savings by curbing unexpected expenses and optimizing operational budgets, positioning businesses for sustained growth and competitiveness in the market.
Common Types of Industrial Machinery
When delving into the realm of industrial machinery, distinct categories such as heavy equipment, manufacturing machinery, and processing units emerge as fundamental pillars of the industrial landscape. Understanding the nuances of these machinery types is paramount in crafting tailored repair and maintenance strategies to ensure optimal functionality and longevity.
Heavy Equipment
Heavy equipment stands as a cornerstone in industrial operations, encompassing varied machinery like cranes, bulldozers, and excavators that are essential for tasks requiring immense power and durability. The key characteristic of heavy equipment lies in its robust construction and capacity to handle heavy loads, making it indispensable in sectors like construction, mining, and logistics. However, the sheer size and complexity of heavy equipment pose challenges in terms of maintenance and repair, necessitating specialized expertise and tailored care routines.
Manufacturing Machinery
Manufacturing machinery forms the bedrock of production facilities, encompassing systems like CNC machines, stamping presses, and conveyors that automate manufacturing processes with precision and speed. The key characteristic of manufacturing machinery lies in its role of transforming raw materials into finished products with consistent quality and efficiency. This machinery thrives on seamless operation and optimized performance to meet production demands, underlining the importance of meticulous maintenance to uphold production standards and output levels.
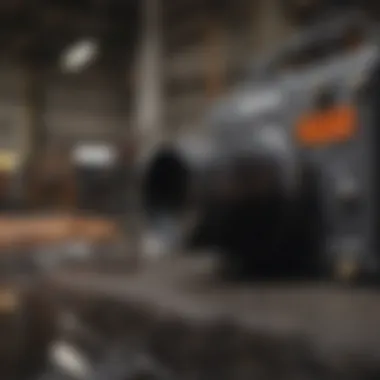
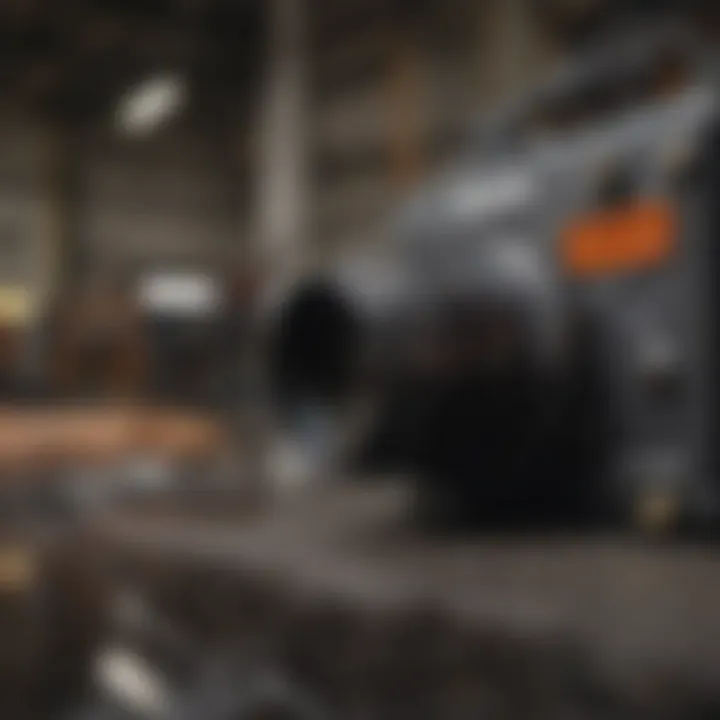
Processing Units
Processing units play a pivotal role in refining raw materials or components to facilitate the production of goods in diverse industries. From chemical reactors to distillation columns, these units are instrumental in extracting, transforming, and synthesizing materials as per specific needs. The key characteristic of processing units lies in their specialized functions tailored to specific industrial processes, necessitating precise monitoring and upkeep to guarantee uninterrupted production cycles and adherence to quality standards.
Implementing Repair Procedures
Implementing Repair Procedures holds immense significance in this detailed examination of industrial machinery repair. It serves as the backbone of efficient operations, ensuring smooth functioning and longevity of the equipment. By focusing on precise implementation methodologies, this section highlights key elements such as scheduled maintenance practices, repair vs. replacement considerations, and meticulous vendor selection. Emphasizing the proactive approach to repairs, this segment delves into the intricacies of routine maintenance, cost-benefit analysis, and the integration of advanced technological upgrades.
Routine Maintenance Practices
Scheduled Inspections
Scheduled inspections play a pivotal role in the overarching goal of maximizing efficiency in industrial machinery repair. These planned assessments provide crucial insights into the current state of equipment, pinpointing potential issues before they escalate into major problems. The key characteristic of scheduled inspections lies in their proactive nature, enabling maintenance teams to preemptively address maintenance needs, thus minimizing downtime and preventing costly breakdowns. Despite their benefits, scheduled inspections do require dedicated resources and time commitment, underscoring the importance of efficient planning and execution.
Lubrication Regimens
Discussing lubrication regimens sheds light on a fundamental aspect of routine maintenance in industrial machinery repair. Proper lubrication is essential for ensuring optimal performance and durability of components, reducing friction, wear, and extending the lifespan of equipment. The key characteristic of lubrication regimens lies in their ability to enhance operational efficiency and forestall premature wear and tear. However, improper lubrication can lead to equipment malfunction and increased maintenance costs, making adherence to recommended regimens crucial for overall system efficacy.
Filter Replacements
Exploring the realm of filter replacements reveals a critical facet of preventive maintenance strategies. Filters play a crucial role in removing contaminants and debris from machinery systems, safeguarding components from damage and preserving operational integrity. The unique feature of filter replacements lies in their ability to maintain optimal performance levels by ensuring clean and efficient operation. While timely filter replacements can prevent system failures and enhance equipment longevity, neglecting this aspect can result in reduced efficiency, increased energy consumption, and potential breakdowns.
Repair Vs. Replacement Considerations
Delving into repair versus replacement considerations provides essential insights into strategic decision-making processes in industrial machinery maintenance. Conducting a thorough cost-benefit analysis is paramount to assessing the most viable option in addressing equipment malfunctions. Environmental impact assessments help gauge the ecological footprint of repair decisions, aligning maintenance practices with sustainability goals. Embracing technological upgrades offers a pathway to improved efficiency, enhanced performance, and future-proofing machinery systems against obsolescence.
Cost-benefit Analysis
The focus on cost-benefit analysis underscores the need for informed decision-making in industrial machinery repair. Evaluating the economic feasibility of repair options against replacement alternatives aids in optimizing resource allocation and minimizing operational disruptions. The key characteristic of cost-benefit analysis lies in its ability to provide a quantitative framework for assessing repair investments, facilitating strategic choices that balance financial considerations with performance outcomes.
Environmental Impact Assessment
Environmental impact assessment plays a pivotal role in shaping repair and maintenance strategies in alignment with sustainability objectives. Considering the ecological consequences of repair actions ensures that operational decisions uphold environmental stewardship principles while mitigating adverse effects on the surroundings. The unique feature of environmental impact assessments lies in their holistic approach towards evaluating the long-term sustainability implications of repair practices, fostering eco-friendly solutions and responsible resource management.
Technological Upgrades
Exploring technological upgrades unveils a realm of innovative solutions to enhance industrial machinery efficiency. Embracing technological advancements enables organizations to streamline operations, improve productivity, and capitalize on cutting-edge developments in the repair industry. The key characteristic of technological upgrades lies in their potential to revolutionize maintenance procedures, incorporating smart technologies, automation, and data-driven insights for superior performance outcomes. While technological upgrades offer substantial benefits in terms of efficiency and operational excellence, their implementation necessitates careful consideration of compatibility, training requirements, and long-term viability.
Vendor Selection and Negotiation
The section on vendor selection and negotiation serves as a guide to navigating supply chain dynamics and optimizing repair service procurement. Adhering to quality assurance standards ensures that vendors meet stringent quality benchmarks, safeguarding operational reliability and performance consistency. Crafting service level agreements establishes clear expectations and accountability parameters between maintenance providers and industrial entities, fostering mutual understanding and service excellence. Implementing effective budget allocation strategies aids in resource optimization, ensuring that repair and maintenance investments align with organizational objectives and financial prudence.
Quality Assurance Standards
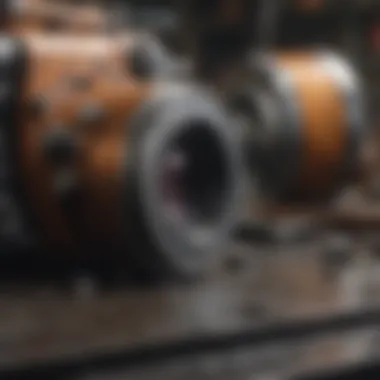
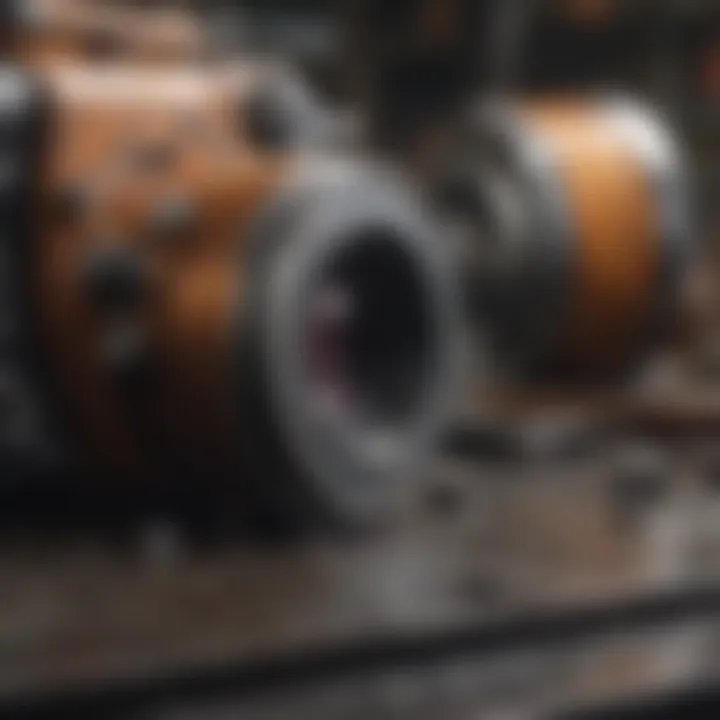
Quality assurance standards delineate the benchmark for evaluating vendor performance and service quality in industrial machinery repair. Adhering to established quality benchmarks guarantees that repairs meet industry-specific standards, promoting operational reliability and customer satisfaction. The key characteristic of quality assurance standards lies in their role in upholding service excellence, instilling confidence in repair outcomes and fostering long-term partnerships with reliable vendors.
Service Level Agreements
Service level agreements establish a contractual framework for defining service expectations, responsibilities, and performance metrics in industrial machinery repair partnerships. By outlining specific deliverables, response times, and escalation procedures, service level agreements ensure transparency and accountability between service providers and clients. The unique feature of service level agreements lies in their ability to formalize service arrangements, minimize dispute resolutions, and enhance overall service quality through shared understanding and communication.
Budget Allocation Strategies
Exploring budget allocation strategies sheds light on the crucial role of financial planning in optimizing repair and maintenance expenditure. Strategically allocating resources ensures that repair investments align with organizational goals, financial constraints, and operational priorities. The key characteristic of budget allocation strategies lies in their capacity to balance short-term repair needs with long-term maintenance requirements, fostering fiscal sustainability and operational resilience. While effective budget allocation enhances resource efficiency and strategic decision-making, overlooking this aspect can lead to cost overruns, operational disruptions, and suboptimal repair outcomes.
Maximizing Efficiency and Productivity
In the realm of industrial machinery repair, the significance of enhancing efficiency and productivity cannot be overstated. It serves as a cornerstone for seamless operations, cost-effectiveness, and prolonged equipment lifespan. By focusing on optimizing equipment performance, companies can streamline their processes, minimize downtimes, and reduce maintenance costs. Emphasizing productivity ensures that every resource is utilized effectively, leading to enhanced output and streamlined workflows.
Optimizing Equipment Performance
- Calibration Procedures: Calibration procedures play a pivotal role in ensuring that machinery functions at peak efficiency. By fine-tuning and aligning equipment according to predefined standards, calibration procedures enhance precision, accuracy, and reliability. The meticulous nature of calibration procedures ensures that equipment operates within optimal parameters, reducing the risk of errors and malfunctions. Despite its time-consuming nature, the benefits of calibration procedures far outweigh the investment, offering enhanced performance and longevity to industrial machinery.
- Operational Parameter Adjustment: Operational parameter adjustment involves tweaking various settings to optimize equipment performance. This customization allows companies to adapt machinery to specific tasks, improving efficiency and output quality. The flexibility offered by operational parameter adjustment enables operators to fine-tune equipment settings based on real-time data and performance feedback. While it requires expertise and monitoring, operational parameter adjustment maximizes equipment effectiveness and minimizes resource wastage.
- Energy Consumption Optimization: Efficient energy consumption is paramount for reducing operational costs and environmental impact. By optimizing energy usage through efficient machinery operation, companies can achieve sustainability goals while enhancing productivity. Energy consumption optimization involves adopting energy-efficient technologies, monitoring energy usage patterns, and implementing smart energy management practices. Despite initial costs, the long-term benefits of energy consumption optimization include reduced carbon footprint, lower utility bills, and compliance with environmental regulations.
Training and Skill Development
- Employee Training Programs: Employee training programs are instrumental in cultivating a skilled workforce capable of complex machinery operation and maintenance. These programs enhance employee competencies, increase operational efficiency, and reduce errors. By providing comprehensive training, companies invest in the professional development of their staff, ensuring seamless machinery operation and minimal downtime.
- Skill Enhancement Workshops: Skill enhancement workshops offer hands-on training opportunities for employees to refine their technical skills and knowledge. These interactive sessions focus on practical scenarios, problem-solving techniques, and best practices in machinery repair and maintenance. By participating in skill enhancement workshops, employees gain valuable insights and expertise, improving overall operational efficiency and equipment performance.
- Certification Courses: Certification courses validate the expertise of employees in specific industrial machinery domains. These courses provide in-depth knowledge, practical skills, and industry recognition, enhancing employee credibility and competency. Companies benefit from certified professionals who can contribute to enhanced productivity, reduced maintenance costs, and higher machinery reliability.
Utilizing Predictive Maintenance Techniques
- Condition Monitoring Technologies: Condition monitoring technologies enable proactive equipment maintenance by assessing real-time data for potential issues. By detecting anomalies and predicting failures, companies can schedule timely maintenance, prevent breakdowns, and optimize machinery performance. The continuous monitoring offered by these technologies ensures early problem detection, reducing repair costs and enhancing overall equipment reliability.
- Predictive Analytics Tools: Predictive analytics tools leverage machine learning algorithms to forecast equipment failures based on historical data and performance trends. By analyzing patterns and predicting future outcomes, companies can implement preemptive maintenance measures, increasing machinery uptime and operational efficiency. The predictive nature of these tools streamlines maintenance processes, minimizes downtime, and extends machinery lifespan.
- Machine Learning Applications: Machine learning applications revolutionize industrial machinery repair by offering predictive maintenance capabilities, anomaly detection, and performance optimization. Through advanced algorithms and data analysis, machine learning applications enhance equipment reliability, reduce maintenance costs, and improve overall operational efficiency. By harnessing the power of machine learning, companies can stay ahead of maintenance needs, reduce reactive repairs, and ensure uninterrupted machinery operation.
Exploring New Technological Advancements
In this section, we delve into the realm of cutting-edge technological advancements that are revolutionizing the landscape of industrial machinery repair. Embracing these innovations is crucial for staying competitive in today's fast-paced industrial sector. The seamless integration of Io T (Internet of Things) in machinery repair has emerged as a game-changer, offering real-time insights into equipment performance and maintenance needs. This not only enhances productivity but also reduces downtime by facilitating predictive maintenance strategies.
Integration of Io
T in Machinery Repair
Smart Sensors Implementation:
Smart Sensors play a pivotal role in Io T-enabled machinery repair by continuously monitoring equipment health and performance metrics. Their ability to gather data on crucial parameters in real-time enables proactive maintenance interventions, optimizing operational efficiency and prolonging machinery lifespan. The non-intrusive nature of Smart Sensors minimizes disruptions to production processes, making them a popular choice for enhancing predictive maintenance practices.
Data Analytics for Performance Optimization:
Data Analytics leverages the vast amount of data collected by Io T devices to identify patterns and trends that can drive performance optimization strategies. By analyzing historical and real-time data, manufacturers can make data-driven decisions to improve operational workflows, minimize inefficiencies, and maximize output. The integration of Data Analytics in machinery repair enhances decision-making processes, leading to more informed maintenance strategies.
Remote Monitoring Solutions:
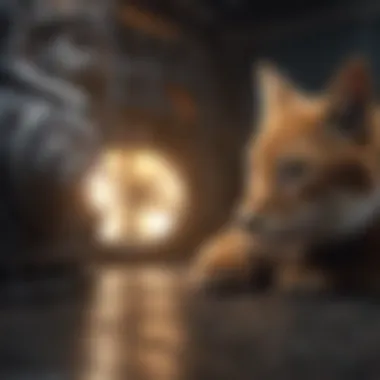
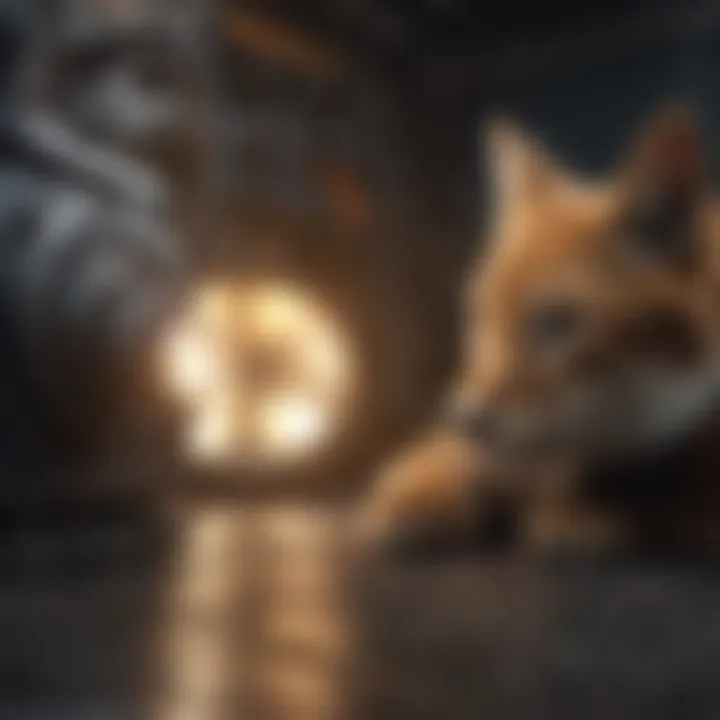
Remote Monitoring Solutions offer the flexibility of monitoring machinery health and performance from any location, transcending geographical constraints. By providing constant updates on equipment status and performance metrics, remote monitoring solutions empower maintenance teams to respond swiftly to emerging issues, reducing the risk of unexpected downtime. This remote access capability streamlines repair procedures, making them an advantageous choice for maintaining operational continuity.
detailed analysis elaboration intricate details meticulous exploration profound insight nuanced perspectives intricate technicalities comprehensive coverage in-depth study thorough examination detailed scrutiny thorough investigation substantial depth detailed evaluation detailed delineation nuanced interpretation intricate examination insightful analysis comprehensive overview extensive review
Sustainable Practices in Industrial Machinery Repair
Sustainable practices in industrial machinery repair are pivotal in maintaining ecological balance while upholding operational efficiency in the industrial sector. Embracing sustainability principles not only reduces environmental impact but also promotes economic viability in the long run. The strategic implementation of sustainable practices encompasses various elements such as circular economy principles, energy conservation measures, and adherence to environmental regulations. By integrating sustainability into repair processes, organizations can contribute significantly to resource conservation and environmental stewardship.
Circular Economy Principles
Recycling Initiatives
Recycling initiatives play a crucial role in the circular economy framework by promoting the reutilization of materials, thereby reducing waste generation and conserving resources. The key characteristic of recycling initiatives lies in their ability to transform discarded materials into valuable inputs for manufacturing processes, fostering a sustainable approach to material utilization. This sustainable practice is a popular choice in industrial machinery repair due to its dual benefit of cost-efficiency and environmental responsibility. Although recycling initiatives require initial investment in infrastructure and processes, the long-term advantages of resource conservation and waste reduction outweigh any potential drawbacks.
Resource Recovery Programs
Resource recovery programs focus on recovering energy or materials from waste streams, allowing for the efficient utilization of resources that would otherwise be discarded. The essence of resource recovery lies in its contribution to minimizing waste production and maximizing resource efficiency within industrial operations. This approach is favored in the context of industrial machinery repair for its capability to transform waste into valuable resources, aligning with the principles of a circular economy. While resource recovery programs require robust monitoring and operational setups, their positive impact on sustainability and resource utilization makes them a valuable addition to industrial repair practices.
Upcycling Practices
Upcycling practices involve repurposing discarded materials to create products of higher quality or value, promoting creativity and resourcefulness in material utilization. The distinguishing feature of upcycling practices is their emphasis on innovative redesigning and upgradation of materials, leading to the development of new, functional products from existing resources. This aspect makes upcycling a favorable choice for industrial machinery repair as it enables organizations to minimize waste generation and reduce the demand for new raw materials. While upcycling practices require strategic planning and creative thinking, their potential for cost savings and environmental impact mitigation renders them advantageous in the realm of sustainable repair methodologies.
Energy Conservation Measures
Efficient Power Consumption Strategies
Efficient power consumption strategies focus on optimizing energy usage within industrial operations to minimize wastage and reduce carbon footprint. The key characteristic of these strategies lies in their ability to streamline energy consumption by implementing efficient technologies and practices, thus enhancing operational sustainability. This approach is a beneficial choice for industrial machinery repair as it not only reduces operational costs but also aligns with environmental conservation goals. Despite the initial investment required for upgrading to energy-efficient systems, the long-term advantages in terms of reduced energy expenses and environmental benefits make efficient power consumption strategies a prudent investment for industrial entities.
Renewable Energy Integration
Renewable energy integration involves incorporating clean energy sources like solar or wind power into industrial operations to reduce reliance on traditional fossil fuels. The inherent characteristic of renewable energy integration is its promotion of sustainable power generation while lowering carbon emissions. This practice is a popular choice for industrial machinery repair due to its dual advantage of environmental sustainability and energy cost savings. Although transitioning to renewable energy may necessitate significant capital outlay initially, the potential for long-term energy savings and environmental responsibility makes renewable energy integration a strategic decision for industrial sustainability.
Waste Heat Utilization
Waste heat utilization focuses on capturing and utilizing heat generated from industrial processes to supplement operational energy needs or system heating requirements, thereby enhancing energy efficiency. The key characteristic of waste heat utilization lies in its capacity to convert thermal energy that would otherwise be wasted into a valuable resource for secondary applications, contributing to resource conservation and operational cost reduction. This approach is a beneficial choice for industrial machinery repair as it not only improves energy efficiency but also aligns with sustainability objectives by maximizing energy utilization. While implementing waste heat utilization systems may involve initial investment and infrastructure modifications, the long-term benefits in terms of energy savings and environmental impact mitigation make this practice a viable option for sustainable industrial operations.
Environmental Compliance and Regulations
Emission Standards Adherence
Emission standards adherence entails compliance with regulations governing the emission of pollutants into the atmosphere, aimed at reducing environmental impact and protecting air quality. The essential characteristic of adherence to emission standards lies in the commitment to limiting harmful emissions through the adoption of emission control technologies and practices. This practice is a beneficial choice for industrial machinery repair as it ensures regulatory compliance and promotes environmental stewardship. While aligning with emission standards may require investments in emission control equipment and monitoring systems, the overall advantages in terms of environmental protection and legal adherence make emission standards adherence a fundamental aspect of sustainable industrial practices.
Waste Disposal Guidelines
Waste disposal guidelines encompass regulations and practices for the safe and environmentally responsible disposal of industrial waste, emphasizing proper waste handling and disposal methods to prevent environmental contamination. The key characteristic of waste disposal guidelines lies in their focus on minimizing environmental impact by ensuring the appropriate treatment and disposal of industrial waste streams. This practice is a vital choice for industrial machinery repair as it mitigates potential environmental risks and fosters a cleaner operating environment. While complying with waste disposal guidelines may involve organizational restructuring and adherence to stringent waste management protocols, the long-term benefits of safeguarding environmental health and operational sustainability make waste disposal guidelines a critical component of sustainable industrial practices.
Pollution Control Measures
Pollution control measures encompass strategies and technologies aimed at reducing pollution levels in industrial settings, focusing on pollutant mitigation and prevention of environmental harm. The unique feature of pollution control measures lies in their effectiveness in minimizing the release of contaminants into the environment through pollution prevention and abatement techniques. This practice is a favorable choice for industrial machinery repair as it promotes environmental responsibility and operational sustainability. Although implementing pollution control measures may require investment in pollution control equipment and periodic monitoring, the overall advantages in terms of environmental protection and sustainable resource management make pollution control measures an indispensable aspect of environmentally sound industrial practices.