Elevating Safety Measures: Unveiling the Impact of Line Stopping Equipment
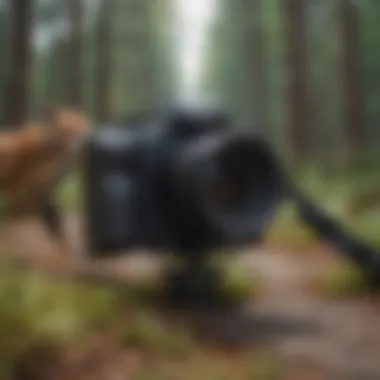
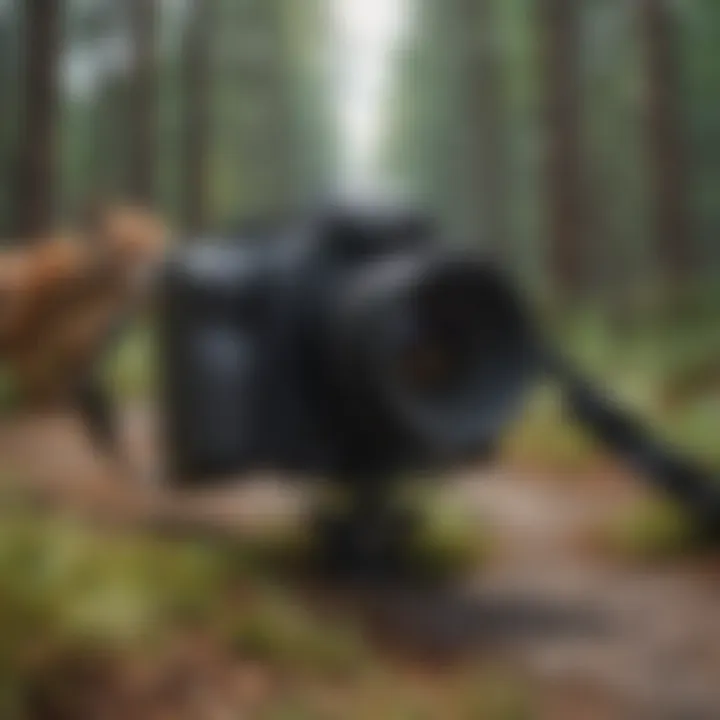
Overview of the Topic
Safety in industrial operations is paramount, with line stopping equipment playing a pivotal role in preventing hazardous situations. Understanding the nuances of different types, functionalities, and applications of line stopping equipment is crucial for maintaining operational efficiency and mitigating risks. In this article, we will delve into the intricate details of enhancing safety through the strategic implementation of line stopping equipment.
Current State and Challenges
Examining the current landscape of industrial safety reveals significant challenges and potential threats that underscore the importance of line stopping equipment. From outdated infrastructure to human errors, various factors contribute to safety concerns in industrial settings. Identifying these challenges is imperative in paving the way for sustainable solutions that prioritize safety and efficiency.
Sustainable Solutions
The quest for sustainable safety solutions necessitates a thorough exploration of best practices and innovative approaches. Utilizing advanced technologies and methodologies can revolutionize safety measures in industries, offering significant improvements in risk management. By showcasing successful case studies and effective resource management techniques, we aim to shed light on the possibilities of harmonizing safety with operational excellence.
Impact and Importance
Analyzing the impact of implementing line stopping equipment unveils its far-reaching implications on ecosystems, communities, and future generations. Integrating safety measures not only safeguards industrial processes but also fosters a culture of responsibility and resilience. Emphasizing the importance of conservation efforts and sustainable resource utilization becomes paramount in ensuring a secure and sustainable future for all stakeholders involved.
Prelude
Line stopping equipment plays a pivotal role in industrial safety protocols, encompassing a critical aspect of risk mitigation and operational continuity. Understanding the nuances of line stopping equipment is paramount in ensuring optimal functioning within industrial settings. This article aims to dissect the various elements of line stopping equipment, shedding light on its significance and applications.
Understanding Line Stopping Equipment
Definition and Purpose
Delving into the core premise of line stopping equipment, its definition encapsulates the methodology of halting fluid flow within pipelines for maintenance, repairs, or expansions. The purpose of this equipment aligns with the strategic pausing of operations without necessitating a complete shutdown. Its key characteristic lies in its ability to isolate a section of the pipeline without affecting the overall system, a fundamental trait lauded for its efficiency and risk mitigation. However, these procedures come with their own set of challenges and complexities, influencing the decision-making process within various industrial operations.
Importance in Industrial Settings
The importance of line stopping equipment in industrial settings cannot be overstated. It serves as a safeguard against potential leaks or ruptures, offering a proactive approach to maintenance and system integrity management. The vital characteristic of this equipment lies in its versatility, catering to a multitude of industries with varying pipeline configurations. Despite its advantages in enhancing safety and operational flexibility, there exist intricacies that demand careful attention to detail to maximize effectiveness. The paramount consideration revolves around balancing efficiency with thorough risk assessments to ensure seamless integration within industrial frameworks.
Key Components of Line Stopping Equipment
Valves
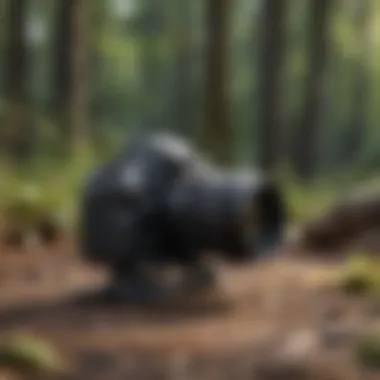
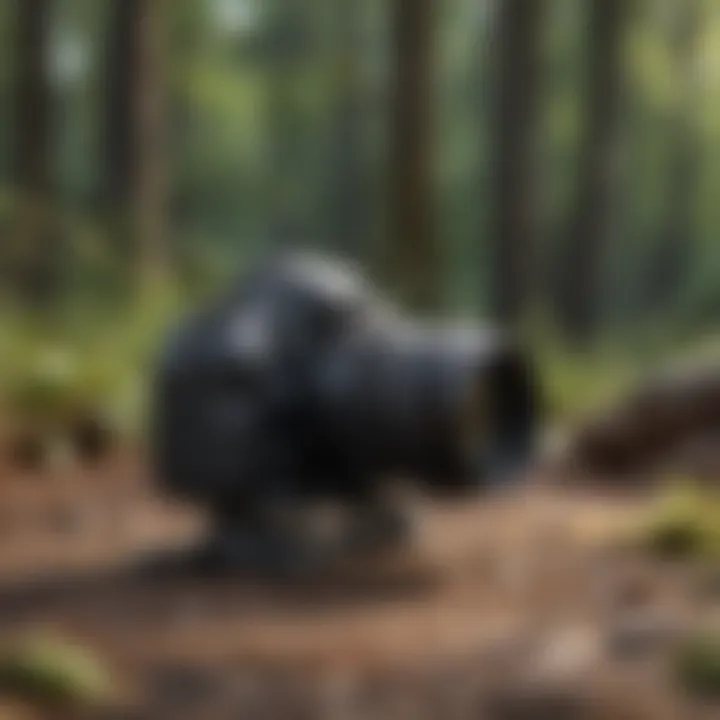
Valves stand as the guardians of controlled fluid flow in line stopping equipment, acting as the primary mechanism for regulating pressure and isolating segments of the pipeline. Their key characteristic lies in the precision of flow control, ensuring accurate maintenance procedures and system interventions. A notable advantage of valves lies in their adaptability to diverse pipeline sizes and compositions, although intricate maintenance requirements may pose operational challenges.
Fittings
Fittings serve as the connective tissue in line stopping equipment, facilitating the seamless integration of valves and control systems within the pipeline infrastructure. Their key characteristic lies in their precision-engineered designs, tailored to specific pipeline dimensions and materials. A notable advantage of fittings rests in their ability to withstand high-pressure environments, ensuring system integrity during critical maintenance operations. However, the selection of fittings necessitates meticulous attention to detail to avoid compatibility issues and leakages.
Control Systems
Control systems act as the orchestrators of line stopping equipment, coordinating the functionalities of valves, fittings, and other components to execute precise maintenance procedures. Their key characteristic lies in the automation of critical processes, minimizing human intervention and optimizing operational efficiency. A notable advantage of control systems lies in their real-time monitoring capabilities, providing essential data for decision-making and risk assessment. However, reliance on complex technology may introduce potential vulnerabilities, mandating robust cybersecurity measures to safeguard operational continuity.
Functionality and Applications
In the realm of industrial operations, the Functionality and Applications of line stopping equipment stand as integral pillars ensuring seamless processes and enhanced safety protocols. By delving into the specific elements of how this equipment operates and its vital role in mitigating risks, the significance of Functionality and Applications becomes vivid. Enabling precise Pressure Regulation, line stopping equipment guarantees a steady flow within the system, averting potential leaks and hazards. On the other hand, through meticulous Flow Control, these tools manage the direction and pace of fluids, optimizing operational efficiency and safety measures. Emphasizing the Functionality and Applications of line stopping equipment unveils its paramount importance in safeguarding industrial structures and personnel.
Operating Principles
Pressure Regulation
Amid the complex tapestry of industrial safety, Pressure Regulation emerges as a critical aspect ensuring stability and control within the operation. By carefully monitoring and adjusting the pressure levels, line stopping equipment creates a secure environment, minimizing the risk of system breakdowns or accidents. The distinguished characteristic of Pressure Regulation lies in its ability to maintain consistent performance under varying conditions, offering a reliable solution for maintaining operational fluidity. While its advantages include enhanced system reliability and reduced downtime, a potential disadvantage could be the need for periodic recalibration to uphold optimum functionality.
Flow Control
In the intricate web of industrial processes, Flow Control plays a pivotal role in governing the movement and distribution of fluids within the system. Through precise management of flow rates and directions, line stopping equipment ensures operational efficiency and safety compliance. The key characteristic of Flow Control lies in its capacity to align fluid movement with specific requirements, optimizing resource utilization and preventing potential bottlenecks. A unique feature of Flow Control is its adaptability to diverse setups, catering to distinct industrial needs effectively. While its advantages encompass improved system performance and regulated resource consumption, potential disadvantages could revolve around intricate calibration requirements and associated maintenance costs.
Industrial Applications
Oil and Gas Pipelines
Within the realm of industrial infrastructure, Oil and Gas Pipelines epitomize critical components where line stopping equipment finds extensive application. The key characteristic of these pipelines is their role in transporting essential resources over vast distances, necessitating the deployment of robust safety measures. As such, line stopping equipment in Oil and Gas Pipelines becomes a crucial element in ensuring seamless operations and risk mitigation. The unique feature of these tools in this context is their ability to isolate specific sections for maintenance or repair, minimizing disruptions and optimizing resource flow. Advantages of utilizing line stopping equipment in Oil and Gas Pipelines include enhanced safety protocols, reduced downtime, and streamlined maintenance processes.
Water Treatment Plants
In the domain of water management and purification, Water Treatment Plants serve as linchpins in ensuring public health and environmental sustainability. The key characteristic of these plants lies in their capacity to treat and distribute clean water to communities, highlighting the indispensable nature of reliable infrastructure. By integrating line stopping equipment into Water Treatment Plants, operators can effectively regulate flow rates and address potential system issues promptly. The unique feature of these tools in this setting is their adaptability to diverse water treatment configurations, catering to varying demands with precision. Benefits of incorporating line stopping equipment in Water Treatment Plants encompass minimized risks of contamination, optimized treatment processes, and enhanced operational resilience.
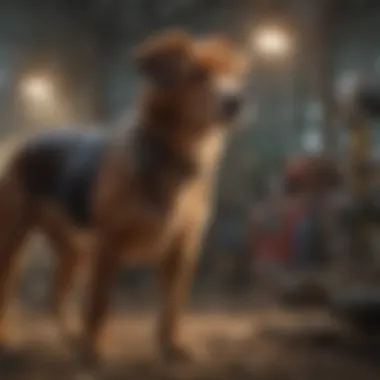
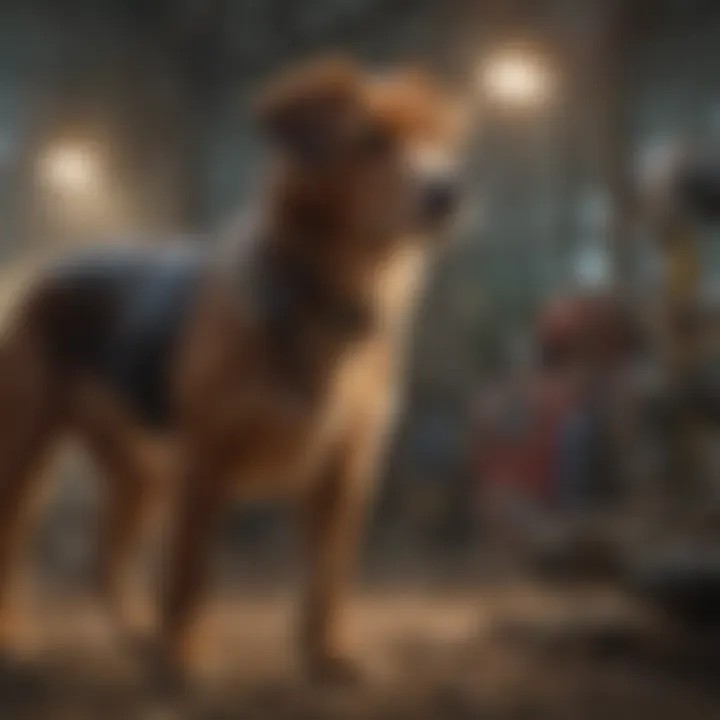
Chemical Processing Facilities
Within the intricate landscape of chemical production, Chemical Processing Facilities emerge as hubs of innovation and production efficiency. The key characteristic of these facilities is their sophisticated infrastructure for manufacturing and processing diverse chemical compounds, underscoring the need for stringent safety measures. By integrating line stopping equipment into Chemical Processing Facilities, operators can effectively regulate fluid flows and isolate sections for maintenance or emergency response. The unique feature of these tools in this environment is their resilience to corrosive substances and varying chemical compositions, ensuring operational continuity under challenging conditions. Advantages of utilizing line stopping equipment in Chemical Processing Facilities encompass enhanced safety protocols, reduced downtime, and streamlined maintenance procedures.
Safety Considerations
Hazard Mitigation
Amidst the bustling landscape of industrial operations, Hazard Mitigation stands as a cornerstone in safeguarding assets, personnel, and the environment. By proactively identifying potential risks and implementing preventative measures, line stopping equipment contributes significantly to hazard mitigation efforts. The key characteristic of Hazard Mitigation lies in its capacity to anticipate and address safety threats before they escalate, fostering a secure operational environment. A unique feature of this approach is its adaptability to diverse industrial settings, encompassing proactive planning and precise execution. Advantages of robust Hazard Mitigation strategies include reduced accident frequencies, minimized financial losses, and enhanced organizational resilience.
Emergency Response Protocols
In the dynamic realm of industrial operations, Emergency Response Protocols play a pivotal role in ensuring swift and effective actions during crises or unforeseen events. Line stopping equipment facilitates the implementation of structured emergency response protocols by enabling quick isolation of problematic areas and fluid containment. The key characteristic of Emergency Response Protocols lies in their ability to streamline coordination among response teams, minimizing response time and optimizing resource allocation. A distinctive feature of this system is its adaptability to evolving emergencies, offering tailored solutions to distinct operational challenges. Benefits of well-defined Emergency Response Protocols incorporate enhanced personnel safety, minimized environmental impact, and expedited recovery processes.
Benefits of Line Stopping Equipment
In the realm of industrial operations, the importance of line stopping equipment cannot be overstated. It serves as a linchpin for enhancing safety and averting potential hazards that could jeopardize operational efficiency. The intricate web of benefits associated with line stopping equipment encompasses a spectrum of elements crucial for ensuring seamless functionality within industrial settings. From the prevention of leakages to the minimization of downtime, each facet plays a pivotal role in fortifying operational integrity and mitigating risks, thus underscoring the indispensability of this advanced technology.
Enhanced Operational Safety
Prevention of Leakages
Minimization of Downtime
In the landscape of industrial operations, minimizing downtime emerges as a critical aspect with far-reaching implications. The ability to curtail downtime translates to uninterrupted workflow and optimized productivity, making it a sought-after attribute in the realm of safety enhancement through line stopping equipment. The key characteristic of downtime minimization rests in its capacity to swiftly address operational hiccups, ensuring a smooth and seamless operational continuum. Despite its advantages in expediting operational processes, downtime minimization necessitates a meticulous approach to maintenance and upkeep to avert potential drawbacks within the operational ecosystem.
Cost-Efficiency and Environmental Impact
Reduction in Repair Costs
One of the pivotal facets of line stopping equipment lies in its capacity to streamline repair costs, thereby ushering in a realm of cost-efficiency. By minimizing the need for extensive repairs and maintenance interventions, it offers a cost-effective solution that harmonizes fiscal prudence with operational efficacy. The unique feature of cost reduction in repair processes not only alleviates financial burdens but also contributes to an optimized operational framework, thus positioning it as a vital component in the line stopping equipment paradigm.
Prevention of Environmental Contamination
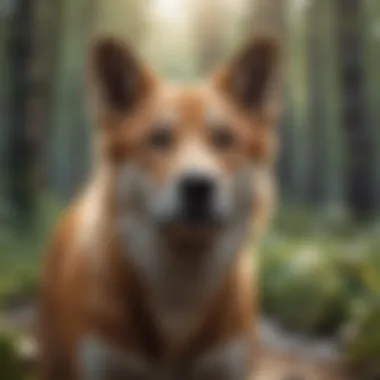
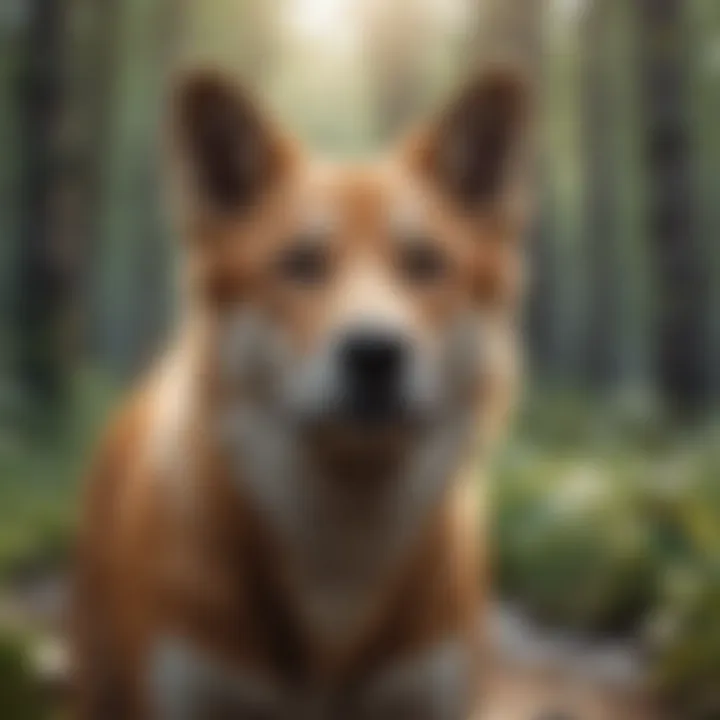
The paradigm of environmental conservation unfurls a critical discourse around the prevention of contamination, an aspect that holds significant implications for industrial safety. Line stopping equipment, through its robust design and functionality, plays a key role in preventing environmental contamination by containing potential leakages and spills, thereby fostering a sustainable operational milieu. Its distinctive feature lies in its capacity to proactively address environmental risks, positioning it as an invaluable asset in fortifying environmental resilience within industrial ecosystems.
Improved System Maintenance
Facilitates Repairs and Inspections
Streamlining the process of repairs and inspections stands as a pivotal attribute of line stopping equipment, accentuating its role in bolstering system maintenance. By offering a seamless mechanism for addressing maintenance requirements, it simplifies the operational landscape and enhances the efficacy of repair and inspection protocols. The key characteristic of this facet lies in its ability to expedite maintenance processes, thereby optimizing operational efficiency and mitigating downtime risks.
Optimizes System Performance
The optimization of system performance represents a key tenet in the domain of operational efficiency, underscoring the significance of line stopping equipment in enhancing system functionality. By fine-tuning operational parameters and ensuring optimal performance metrics, it elevates system operability to newer heights, thereby fostering a comprehensive framework for sustainable industrial operations. The unique feature of performance optimization in system maintenance not only enhances productivity but also augments the operational integrity within industrial settings, positioning line stopping equipment as a vital cog in the machinery of operational excellence.
Future Trends and Innovations
Line stopping equipment plays a pivotal role in enhancing safety and operational efficiency in various industrial settings. As technology continues to evolve, future trends and innovations in this field are of paramount importance. Understanding the strides made in automation and remote monitoring is crucial for staying ahead in safety practices. Automation, particularly through IoT integration, revolutionizes how line stopping equipment is monitored and controlled. The seamless connection between devices enables real-time data transmission to operators, enhancing decision-making and response times.
Automation and Remote Monitoring
IoT Integration
IoT integration stands out as a game-changer in the realm of line stopping equipment. Its ability to interconnect devices and gather data remotely transforms traditional safety protocols. The key advantage of IoT integration lies in its capacity to provide predictive insights into equipment performance. By collecting and analyzing data in real-time, operators can anticipate maintenance needs and detect potential issues before they escalate, thereby minimizing downtime and increasing efficiency. One notable feature of IoT integration is its adaptability to diverse industrial environments, making it a popular choice for enhancing safety practices.
Predictive Maintenance Technologies
Another critical aspect of future trends is the integration of predictive maintenance technologies. By utilizing sophisticated algorithms and machine learning capabilities, predictive maintenance systems forecast equipment failures based on historical data and performance patterns. This proactive approach enables proactive maintenance scheduling, avoiding costly breakdowns and optimizing operational uptime. The unique feature of predictive maintenance technologies lies in their ability to prioritize maintenance tasks based on criticality, ensuring resources are allocated efficiently for maximum impact.
Advancements in Material Technology
In parallel with digital innovations, advancements in material technology have also catalyzed improvements in line stopping equipment. Durable composite materials have emerged as a resilient choice, offering enhanced corrosion resistance and durability. The key characteristic of durable composite materials is their ability to withstand harsh environmental conditions, prolonging equipment lifespan and reducing replacement costs. Despite their initial higher cost, the long-term advantages of these materials outweigh the investment, making them a preferred option for critical applications.
Corrosion-Resistant Coatings
Corrosion-resistant coatings represent another milestone in material technology, particularly in safeguarding line stopping equipment against corrosive substances and external elements. These coatings create a protective barrier, preventing degradation due to chemical exposure or environmental factors. The key characteristic of corrosion-resistant coatings is their ability to maintain equipment integrity over an extended period, reducing the risk of leaks and malfunctions. While these coatings require specialized application processes, their long-term benefits in preventing equipment deterioration justify the additional effort and cost.
Regulatory Compliance and Standards
Maintaining compliance with safety guidelines and industry standards is non-negotiable when it comes to line stopping equipment. Adherence to safety guidelines ensures that operations meet stringent safety criteria, safeguarding personnel and assets. The key characteristic of adhering to safety guidelines lies in the systematic approach to risk assessment and mitigation, prioritizing safety above all else. The unique feature of safety guidelines is their adaptability to evolving safety requirements, keeping pace with industry advancements and best practices for continuous improvement.
Industry Certification Requirements
Meeting industry certification requirements is essential for demonstrating the reliability and quality of line stopping equipment. These requirements serve as benchmarks for assessing product performance and adherence to industry standards. The key characteristic of industry certification requirements is their endorsement of product integrity and safety compliance, instilling confidence in end-users. While navigating certification processes may be time-consuming, the advantages of gaining industry recognition and customer trust outweigh the initial challenges, positioning products competitively in the market.