Mastering Drivecon VFD Efficiency for Optimal Industrial Performance
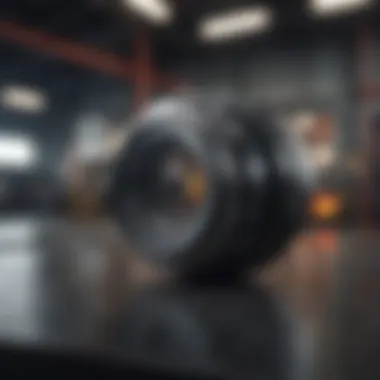
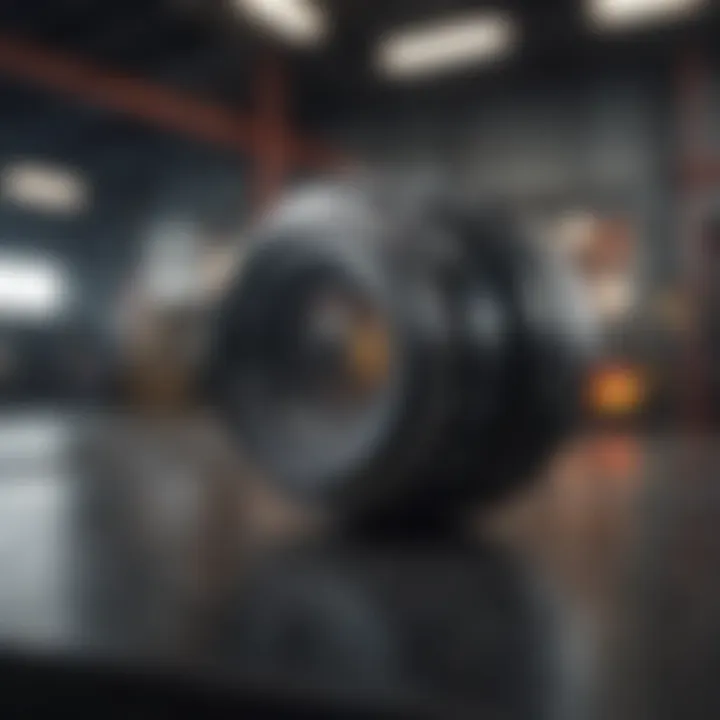
Overview of the Topic
At the core of industrial operations lies the critical component of Drivecon Variable Frequency Drives (VFDs), pivotal in ensuring optimal efficiency and performance. The intricate workings of VFDs hold the key to significant energy savings and operational enhancements that can revolutionize industrial practices. Understanding the nuances of Drivecon VFDs is paramount for industry professionals seeking to maximize their systems' potential.
Current Status and Challenges
The current landscape of industrial applications grapples with the challenge of balancing operational demands with energy efficiency goals. Drivecon VFDs, while offering immense potential for optimization, also face obstacles such as compatibility issues with existing systems and the need for specialized knowledge to unlock their full capabilities. Navigating these challenges requires a deep dive into VFD operation and the implementation of strategic solutions.
Sustainable Solutions
Unlocking the true efficiency of Drivecon VFDs necessitates the adoption of sustainable practices that harness the full scope of their capabilities. From integrating advanced control strategies to incorporating energy-efficient technologies, there exists a myriad of solutions to elevate VFD performance. Real-world case studies exemplify how innovative approaches can lead to substantial energy savings and operational enhancements, paving the way for a sustainable industrial landscape.
Impact and Importance
The impact of Drivecon VFD efficiency transcends individual industrial setups to resonate on a broader scale, impacting ecosystems, communities, and future generations. By optimizing VFDs, industries can mitigate their environmental footprint, reduce energy consumption, and contribute to a more sustainable future. Emphasizing the importance of efficient VFD utilization underscores the critical role that industrial stakeholders play in conserving resources and fostering a greener tomorrow.
Introduction to Drivecon VFDs:
In the realm of industrial applications, the foundation of efficiency lies in understanding the intricate mechanisms of Drivecon Variable Frequency Drives (VFDs). These cutting-edge devices herald a new era of precision control and energy optimization, making them indispensable in modern industrial setups. The quintessence of this section orbits around dissecting the core components and functionalities of Drivecon VFDs, shedding light on their pivotal role in streamlining operations and maximizing productivity.
Understanding Variable Frequency Drives (VFDs):
Principles of VFD Operation:
Diving into the operational heart of Variable Frequency Drives (VFDs), we uncover the fundamental principles that govern their functionality. The crux of VFD operation lies in their ability to regulate motor speed by adjusting the frequency of the input power supplied to the motor. This dynamic process not only enhances operational efficiency but also mitigates energy wastage, positioning VFDs as frontrunners in the realm of industrial automation. The innate flexibility of VFDs in tailoring motor speed to match varying load requirements underscores their indispensability in diverse industrial settings.
Benefits of VFDs in Industrial Applications:
The advantages of integrating VFDs in industrial applications reverberate across multidimensional vectors, transcending mere operational enhancements. From substantial energy savings to improved process control, the benefits of VFDs are multifaceted. By affording operators the leeway to fine-tune motor speeds with surgical precision, VFDs pave the way for unparalleled operational dexterity and resource optimization. Despite their myriad advantages, nuanced considerations regarding installation and programming underscore the importance of strategic deployment to harness the full potential of VFDs.
Overview of Drivecon VFD Technology:
Key Features of Drivecon VFDs:
At the nucleus of Drivecon VFD technology lies a confluence of innovation and reliability, encapsulated in a suite of defining features. The spectrum of key features encompasses robust motor control algorithms, high-fidelity sensors, and intuitive interfaces, amalgamating into a powerhouse of operational prowess. The integration of advanced technologies like regenerative braking and harmonic mitigation underscores Drivecon VFDs' commitment to operational efficiency and sustainability, setting a new benchmark in the domain of industrial automation.
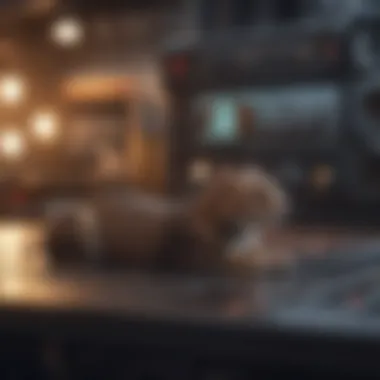
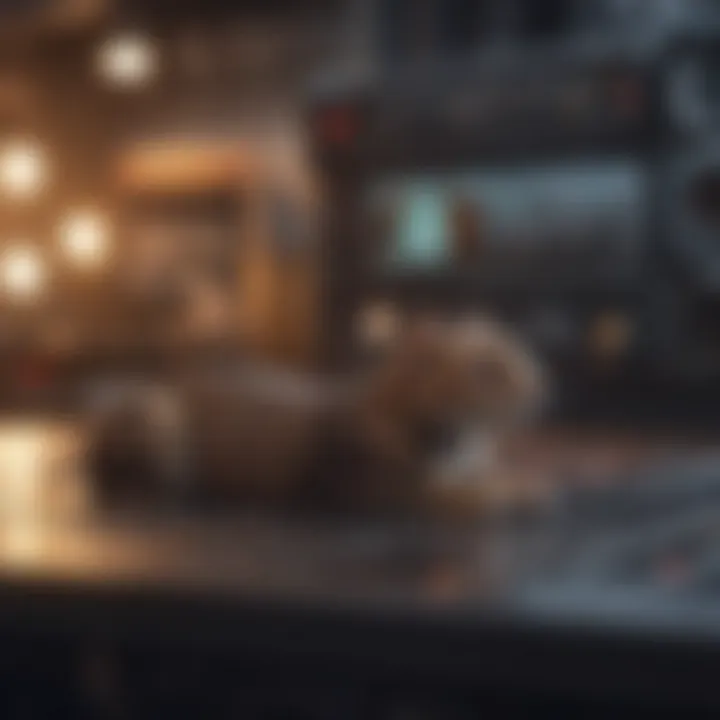
Applications in Various Industries:
The versatility of Drivecon VFDs finds manifestation in a myriad of industrial domains, ranging from manufacturing to wastewater treatment facilities. By seamlessly adapting to the unique requisites of diverse sectors, Drivecon VFDs emerge as veritable workhorses of industrial automation. Their capacity to optimize processes, minimize downtime, and enhance equipment longevity transcends industry-specific boundaries, making them a universal embodiment of efficiency and reliability in the contemporary industrial landscape.
Optimizing Drivecon VFD Performance
Optimizing Drivecon VFD Performance is a critical aspect within the realm of industrial applications that warrants meticulous attention. By delving into this facet, we unlock a realm of opportunities to maximize operational efficiencies and elevate performance benchmarks. The optimization of Drivecon VFDs facilitates a seamless orchestration of machinery, leading to enhanced productivity and resource management. Exploring this topic sheds light on the intricate mechanisms that drive industrial operations towards sustainable growth.
Efficiency Enhancement Techniques
Load Matching and Speed Control
Load Matching and Speed Control play a pivotal role in fine-tuning the operations of Drivecon VFDs. This tandem approach ensures that the load requirements align harmoniously with the system's speed control parameters, optimizing energy consumption and operational output. The synergy between load matching and speed control yields precise control over machinery, fostering a dynamic environment where efficiency thrives. Embracing these techniques empowers industrial setups to achieve unparalleled levels of performance and responsiveness in a controlled setting.
Energy-Saving Strategies
Energy-Saving Strategies constitute a fundamental pillar in the quest for VFD optimization. By integrating energy-saving strategies into the operational framework, industries can curtail wastage and elevate their sustainability credentials. These strategies encompass a spectrum of methodologies aimed at minimizing energy expenditures without compromising output quality. Implementing energy-saving strategies not only bolsters cost-effectiveness but also aligns operations with eco-friendly practices, positioning businesses as stewards of resource-conscious manufacturing.
Maintenance Best Practices
Regular Inspections and Testing
Regular inspections and testing emerge as the cornerstone of proactive maintenance for Drivecon VFD systems. These practices serve as early detectors of potential faults or inefficiencies, preempting operational disruptions and enhancing system longevity. By adhering to regular inspection protocols, industrial operators ensure the seamless functionality of VFDs, mitigating risks associated with downtime and malfunctions. The strategic integration of routine inspections and testing fosters a culture of reliability and performance excellence within industrial setups.
Troubleshooting Common Issues
Efficient troubleshooting of common issues stands as a testament to the resilience and adaptability of industrial systems incorporating Drivecon VFDs. Identifying and resolving common challenges swiftly bolsters operational continuity and minimizes the impact of disruptions. With a keen focus on troubleshooting common issues, industrial stakeholders fortify their operational preparedness, navigating complexities with precision and agility. This meticulous approach not only streamlines maintenance processes but also cultivates a culture of continuous improvement and resilience in industrial landscapes.
Advanced Control Strategies for Drivecon VFDs
The crux of elevating Drivecon Variable Frequency Drives (VFDs) lies in the mastery of advanced control strategies. In this exhaustive segment, we delve deep into the pivotal role that these strategies play in ensuring optimal VFD performance. By honing in on specific elements such as Sensorless Vector Control and Field-Oriented Control (FOC), we decipher the intricate web of benefits and considerations that underlie the realm of advanced VFD control strategies. The fusion of advanced control techniques with Drivecon VFD technology propels industrial operations towards heightened efficiency and precision.
Sensorless Vector Control
Principles and Implementation
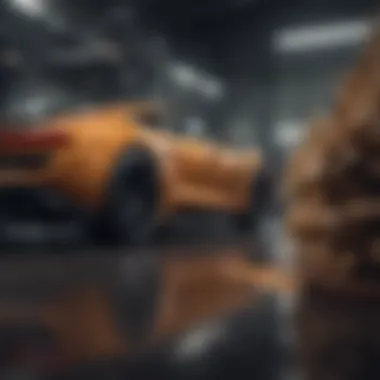
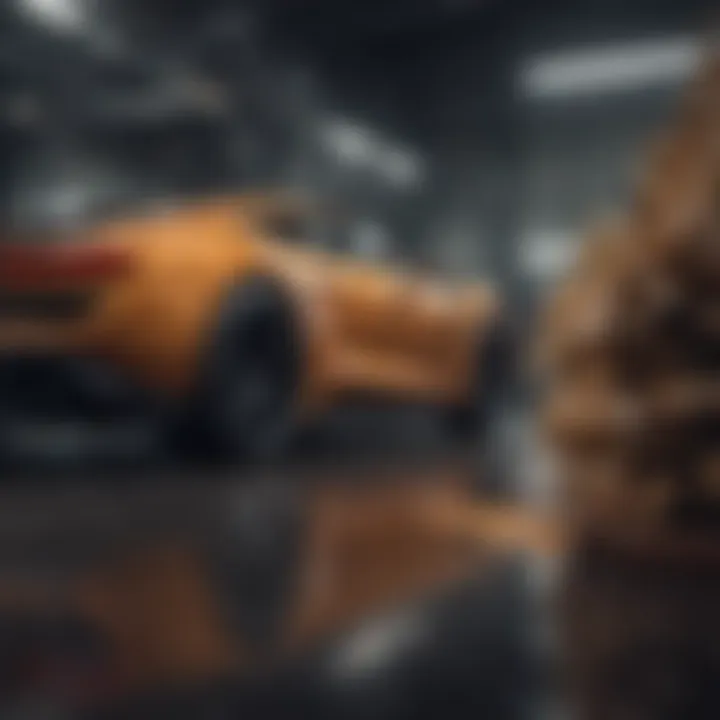
Embarking on the voyage of Sensorless Vector Control steers us towards a realm where precision and innovation converge. The backbone of this methodology lies in its adeptness at deciphering and manipulating motor control without the need for cumbersome sensors. The idiosyncratic feature of Sensorless Vector Control lies in its ability to enhance control accuracy while minimizing complexity. This unique facet not only streamlines operational efficiency but also presents a cost-effective solution, making it a formidable choice in the realm of Drivecon VFD optimization.
Advantages in Precision Control
Unveiling the domain of precision control, we uncover the myriad advantages ensconced in Sensorless Vector Control. The crux of its prowess rests in its ability to confer a level of precision that eclipses conventional control strategies, marking a paradigm shift in VFD optimization. The key characteristic of precision control bestowed by Sensorless Vector Control amplifies operational accuracy to unforeseen levels, heralding a new era of operational finesse. Nonetheless, as with all mechanisms, this approach entails certain trade-offs, which necessitate a judicious evaluation of benefits and potential drawbacks within this article's context.
Field-Oriented Control (FOC)
Operating Principles and Benefits
Navigating through the intricacies of Field-Oriented Control (FOC), we unravel a tapestry woven with a harmonious blend of operating principles and tangible benefits. The hallmark of FOC lies in its unwavering dedication to aligning motor currents with flux, ensuring a symphony of control precision. This key characteristic presents Field-Oriented Control as a beacon of efficiency and reliability within our discourse, showcasing why it stands as a preferred choice in optimally maneuvering Drivecon VFDs. The nuanced feature set encapsulated within the operating principles and benefits of FOC offers a nuanced perspective on its role in our article, shedding light on its advantages and potential limitations.
Integration with Drivecon VFDs
Delving into the symbiotic relationship between Field-Oriented Control (FOC) and Drivecon VFDs, we unearth a seamless integration that amplifies operational prowess. The core allure of this integration lies in its ability to synergize the robust features of FOC with the intrinsic capabilities of Drivecon VFDs, culminating in a potent concoction of performance enhancement. Highlighting the specific characteristics that render this integration invaluable, we discern why it emerges as a prominent choice for our overarching goal. However, as with any amalgamation of technologies, it is imperative to dissect both the advantages and potential drawbacks offered by this integration within the contextual confines of this article.
Ensuring Safety and Compliance
In navigating the intricate world of industrial applications, Ensuring Safety and Compliance stands as a paramount consideration. Safety protocols and compliance measures play a pivotal role in maintaining a secure working environment and adhering to legal standards. Addressing safety concerns proactively not only safeguards personnel and assets but also mitigates potential risks and liabilities. Compliance with regulations ensures that operations run smoothly within the boundaries of the law, fostering a culture of responsibility and accountability.
Regulatory Standards and Guidelines
OSHA Requirements
Emphasizing the Occupational Safety and Health Administration (OSHA) requirements is fundamental for workplace safety. OSHA regulations set forth comprehensive guidelines to protect workers from occupational hazards, encompassing various aspects such as electrical safety, personal protective equipment, and emergency response procedures. Complying with OSHA standards demonstrates a commitment to employee welfare and regulatory compliance, promoting a culture of safety consciousness and risk mitigation. The stringent nature of OSHA requirements underscores the commitment to ensuring a secure work environment, reducing the likelihood of accidents and injuries.
Industry-Specific Regulations
Navigating industry-specific regulations tailored to the nuances of particular sectors is crucial for operational integrity. These regulations address specific hazards and operational practices inherent to certain industries, supplementing general safety guidelines with specialized requirements. Adhering to industry-specific regulations enhances safety protocols by customizing measures to address industry-specific risks effectively. By embracing industry-specific regulations, organizations demonstrate a keen understanding of sector-specific challenges and a proactive approach to mitigating potential hazards, ultimately fostering a safer and more compliant work environment.
Safety Protocols for Drivecon VFD Installations
Emergency Shutdown Procedures
Efficiently executing emergency shutdown procedures is critical for preventing accidents and equipment damage. Establishing clear protocols for rapid response in emergencies ensures quick intervention and containment of potentially hazardous situations. Emergency shutdown procedures prioritize swift actions to mitigate risks promptly, safeguarding personnel and equipment from harm. By implementing robust emergency shutdown procedures, organizations demonstrate a commitment to proactive risk management and the safety of all stakeholders.
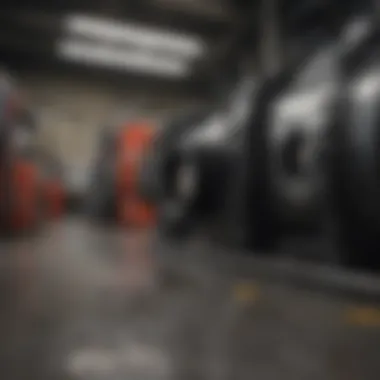
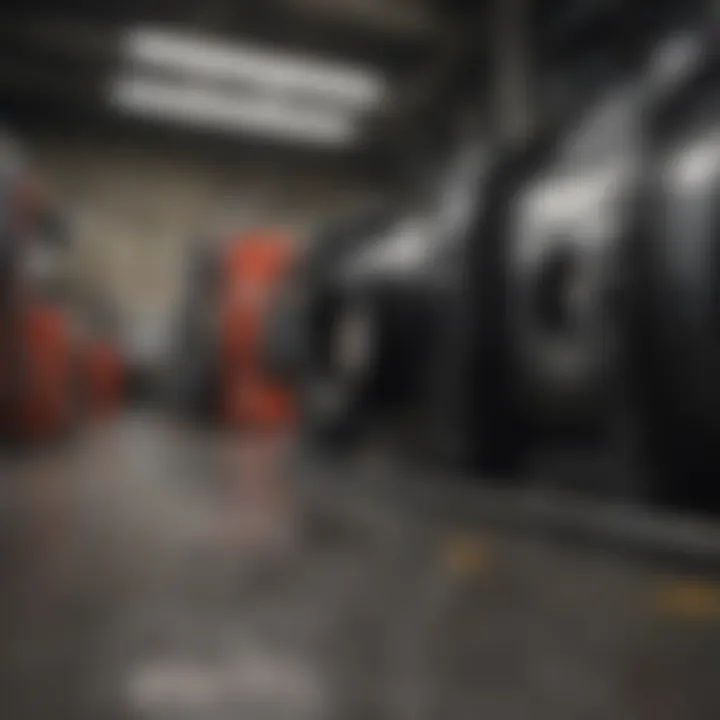
Overcurrent Protection Measures
Implementing overcurrent protection measures is essential for safeguarding Drivecon VFD installations. These measures prevent equipment damage and minimize the risk of electrical hazards by detecting and responding to excessive currents. Overcurrent protection measures ensure the longevity and optimal performance of VFD systems, reducing downtime and maintenance costs. By integrating effective overcurrent protection measures, organizations enhance the reliability and safety of their Drivecon VFD installations, ensuring uninterrupted operational efficiency.
Integration of Drivecon VFDs with Control Systems
In the realm of industrial applications, the integration of Drivecon Variable Frequency Drives (VFDs) with Control Systems plays a pivotal role in enhancing operational efficiency and precision. By harmoniously blending VFD technology with control systems, organizations can achieve seamless control over their processes, ensuring optimal performance and energy utilization. The synergy between Drivecon VFDs and control systems empowers businesses to streamline operations, respond promptly to fluctuations in demand, and maintain consistent output quality. This integration also facilitates real-time monitoring and adjustment, thereby maximizing productivity and reducing downtime, which are paramount in the competitive industrial landscape.
PLC Integration for Seamless Control
Interfacing with Programmable Logic Controllers
Interfacing Drivecon VFDs with Programmable Logic Controllers (PLCs) symbolizes a cornerstone in the quest for operational fluidity and efficiency. The synchronization between VFDs and PLCs enables precise coordination of industrial processes, allowing for intricate control over speed, torque, and other critical parameters. The compatibility of Drivecon VFDs with PLCs ensures a streamlined communication pathway, fostering quick response times and minimizing latency in control signals. This amalgamation grants operators the ability to program complex logic sequences, automate tasks, and dynamically adjust VFD settings within the overarching control framework. The robust interplay between VFDs and PLCs not only optimizes energy consumption and performance but also paves the way for enhanced operational intelligence and adaptability in industrial environments.
Data Exchange Protocols
The implementation of efficient data exchange protocols within the realm of Drivecon VFD integration holds immense significance for comprehensive data management and analysis. Data exchange protocols serve as the nerve center for transmitting critical operational information between VFDs and control systems, facilitating seamless data flow and synchronization. By adhering to standardized communication protocols, such as Modbus or EthernetIP, organizations can achieve interoperability between diverse industrial devices and systems. This standardization ensures data integrity, security, and accessibility, allowing for streamlined integration and configuration of Drivecon VFDs within existing control infrastructures. Moreover, leveraging data exchange protocols enhances diagnostic capabilities, supports predictive maintenance strategies, and empowers decision-making processes through the availability of real-time operational insights. The judicious application of data exchange protocols not only fosters operational transparency and efficiency but also fortifies the foundation for advanced data analytics and process optimization in industrial settings.
Future Trends in Drivecon VFD Technology
Future Trends in Drivecon VFD Technology play a pivotal role in shaping the trajectory of industrial processes. Understanding and adapting to these upcoming trends are crucial for organizations striving to stay ahead in a rapidly evolving landscape. By delving into emergent technologies and methodologies, businesses can enhance operational efficiency, reduce costs, and improve sustainability practices. The exploration of future trends provides a roadmap for innovation and growth, fostering a competitive edge in the market.
Emerging Innovations in VFD Design
Enhanced Energy Efficiency Features
Enhanced Energy Efficiency Features represent a breakthrough in VFD design, revolutionizing energy consumption patterns within industrial applications. By prioritizing energy efficiency, businesses can significantly reduce operational costs and environmental impact. The key characteristic of Enhanced Energy Efficiency Features lies in their ability to optimize power usage dynamically, aligning with varying load demands seamlessly. This adaptability enables streamlined operations and promotes a more sustainable approach to energy utilization. Despite certain challenges, such as initial implementation costs, the long-term benefits of Enhanced Energy Efficiency Features outweigh the investment, making them a strategic choice for organizations seeking to maximize efficiency.
Digital Twin Technology Applications
Digital Twin Technology Applications introduce a paradigm shift in VFD functionality, offering unprecedented insights and control capabilities. By creating virtual replicas of physical VFD systems, organizations can simulate and optimize performance in real-time, enhancing operational efficiency and predictive maintenance practices. The key characteristic of Digital Twin Technology lies in its ability to monitor and analyze VFD performance data with remarkable accuracy, enabling proactive decision-making and preemptive fault detection. While the integration of Digital Twin Technology may require initial adjustments, the long-term advantages, such as reduced downtime and enhanced productivity, make it a valuable addition to industrial setups.
Sustainable Practices in VFD Manufacturing
Recyclable Materials
The integration of Recyclable Materials in VFD manufacturing signifies a commitment to sustainability and environmental responsibility. By utilizing materials that can be repurposed or recycled, manufacturers contribute to circular economy practices, reducing waste and resource depletion. The key characteristic of Recyclable Materials lies in their ability to minimize environmental impact throughout the VFD lifecycle, from production to disposal. While incorporating Recyclable Materials may pose logistical challenges initially, the environmental benefits and positive reputation associated with sustainable practices make them an advantageous choice for VFD manufacturers.
Carbon Footprint Reduction Initiatives
Carbon Footprint Reduction Initiatives are instrumental in mitigating the environmental impact of VFD manufacturing processes. By implementing measures to reduce carbon emissions and energy consumption, manufacturers can align with global sustainability goals and regulatory requirements. The key characteristic of Carbon Footprint Reduction Initiatives lies in their capacity to promote eco-friendly practices, leading to cleaner production methods and lower greenhouse gas emissions. Despite potential constraints, such as transition costs, the long-term advantages of Carbon Footprint Reduction Initiatives, including enhanced corporate social responsibility and market positioning, position them as indispensable strategies for VFD manufacturers.